一线质检员必须掌握的7个质量工具
一线的质量人,最怕什么?不是出了问题,而是出了问题你自己搞不清楚原因在哪,只能“修一修”“调一调”“观察看看”,久而久之,一直在这个岗位得不到成长。那能力提升最重要的一步就是,提高数据化思维与分析能力。
而QC七大手法,就是为了解决这个问题而生的。它们是:检查表、排列图(柏拉图)、因果图(鱼骨图)、直方图、控制图、散布图、层别法。工具虽老,但一点不“落后”——只要你用得起来,能解决现场的90%的问题。
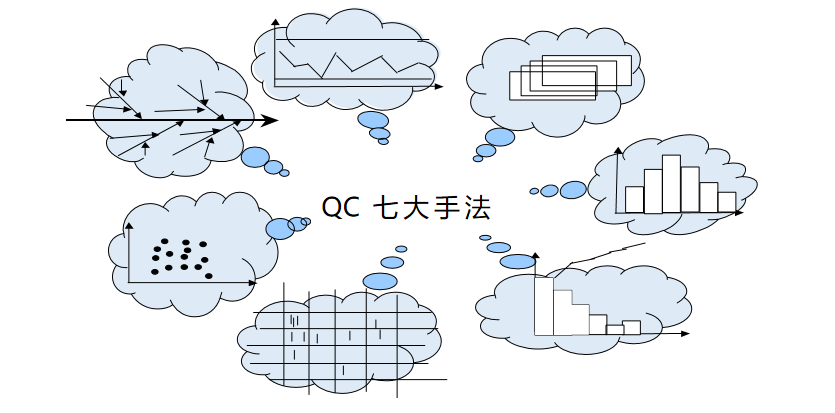
一、检查表:一切分析的数据源头
你没数据,后面所有的分析都是空谈。
在设备、产品或工序中,检查表就是用来记录问题类型与频率的最基础工具。你可以用它统计点检项、缺陷数、不良现象发生时间、班次、机台、人员等等。
例如“设备点检卡”和“出门检查清单”就是典型应用,一横一竖结构清晰,数据可追溯。
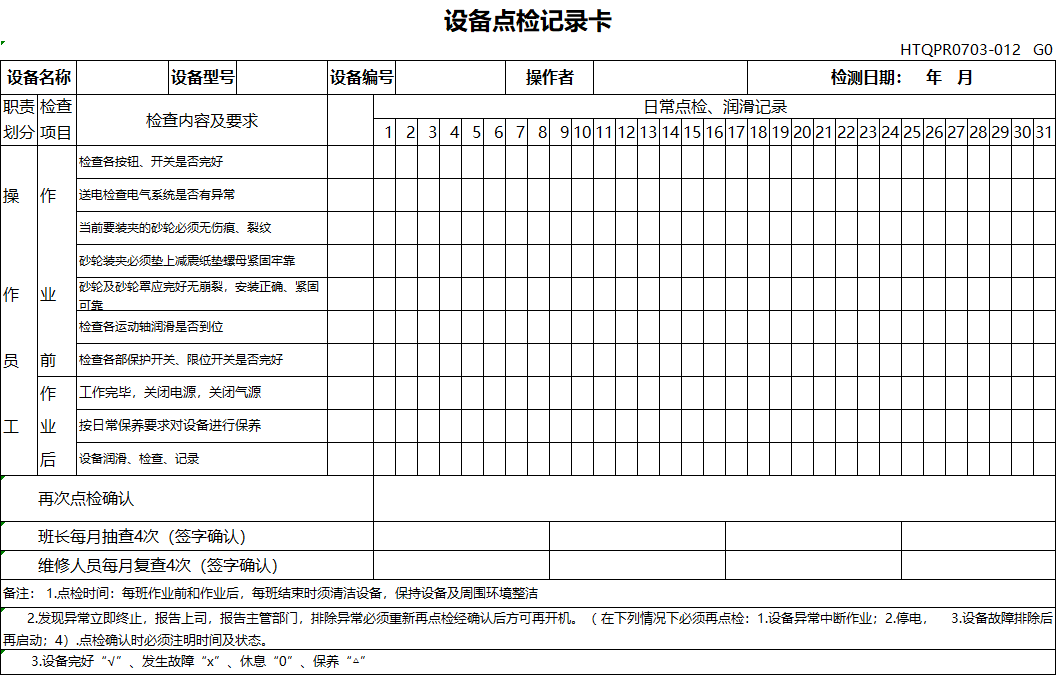
重点应用:
班前确认、设备点检、产品抽检记录 后续用于制作排列图、直方图、控制图的基础数据源
二、排列图(柏拉图):乱中有序中找出优先级
很多质检员常常面临一个问题:今天这个不良也多,那个也有,哪个先处理?
这时候,用排列图(或称柏拉图)可以一目了然地看出问题集中在哪儿,典型的80/20法则——抓住头部20%的问题,解决80%的影响。
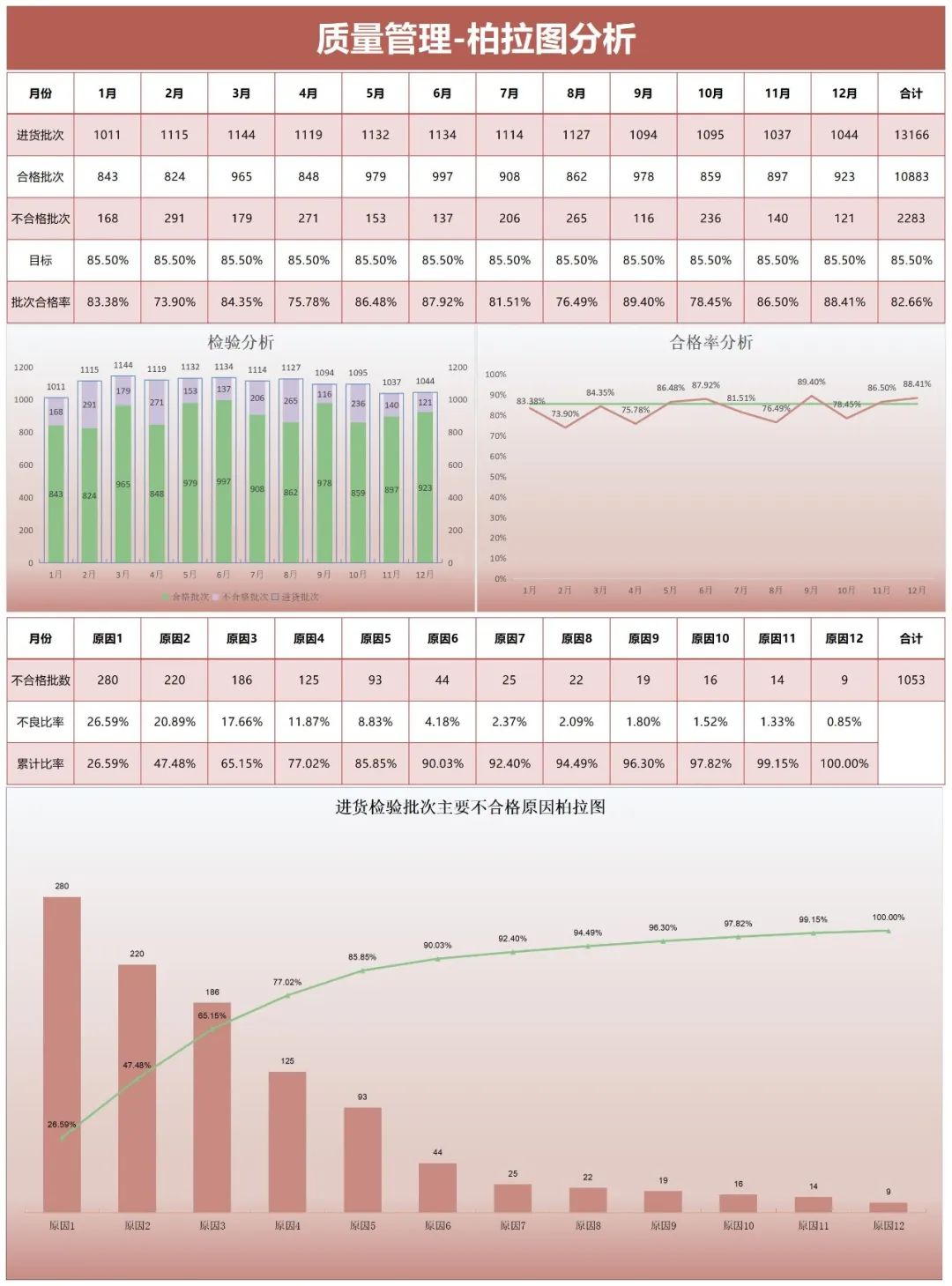
实际用途:
不良TOP3分析 年度、季度质量改善方向制定 与鱼骨图联合使用进行根因分析
三、因果图(鱼骨图):从多个角度系统分析问题根源
问题出现了,如何找根因?光靠经验判断远远不够。
鱼骨图(因果图)就是为了系统分析问题产生的可能原因而生的。常用“5M1E”六大类(人、机、料、法、环、测)进行展开,再逐一验证。
关键要点:
应用在重复性问题的原因分析上 和头脑风暴法结合使用 常作为QC Story中的“要因分析”步骤
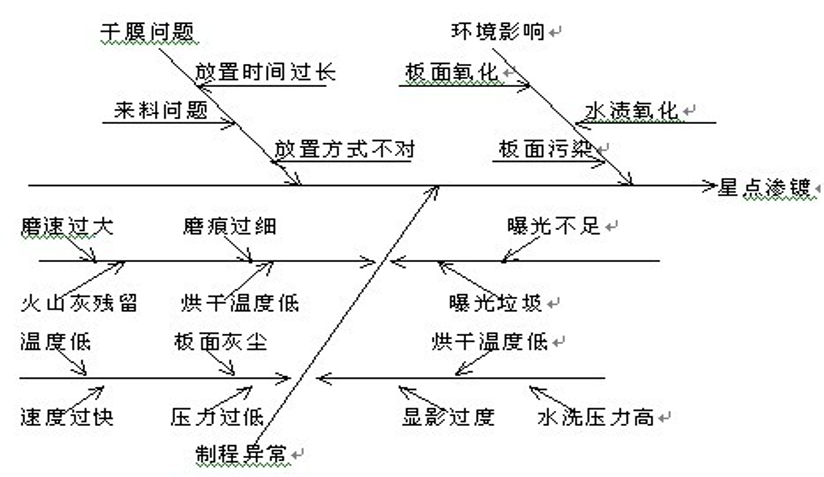
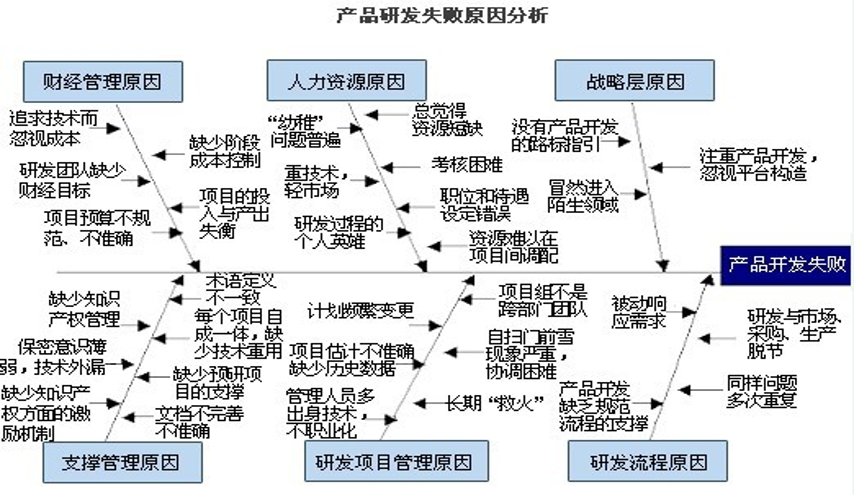
四、直方图:数据波动看得见,分布状态一目了然
有些问题,不是不良,而是“接近不良”。比如尺寸数据虽然没超差,但快到边界了——你感知不到,就容易出风险。
直方图能将大量数据按区间集中展示,判断是否偏移中心或呈异常分布。
建议用途:
关键尺寸数据月度统计分析 和控制图联用,判断过程是否偏离 检验图形是否符合“正态分布”
五、控制图:不是报警才叫异常,趋势就是预警
控制图的真正意义在于:及时识别出“尚未超标”的异常趋势。这在SPC(统计过程控制)中至关重要。

单点超3σ; 连续7点在同一侧; 连续6点单向上升/下降; 2/3点超2σ、4/5点超1σ等。
这些不是“事后处理”,而是“提前预警”。
关键建议:
每个关键参数建立X-bar控制图 对异常规则进行一线培训,现场识别趋势 联动鱼骨图追查异常点背后的根因
六、散布图:变量间有关联吗?画个图就知道
在制造现场,很多问题不是孤立发生的,而是受两个变量的交互影响,比如温度 vs 粘接强度、设备老化 vs 尺寸波动。
散布图能帮助你判断变量间是否存在线性关系。

常见场景:
操作员经验 vs 产品不良率 环境湿度 vs 喷涂效果 原料批次 vs 成品强度
“一旦你发现显著相关性,就可以用作过程监控点,提前管控。
七、层别法
层别法也叫分层法,目的是“把混在一起的数据拆开看”,从而发现问题集中在哪一层。
比如不良率为5%,你拆开看会发现:
白班2%,夜班8%; 新人操作10%,老员工1%; A机台3%,B机台9%。
一看就明白问题在哪儿。这个比“整体平均”要有用太多。
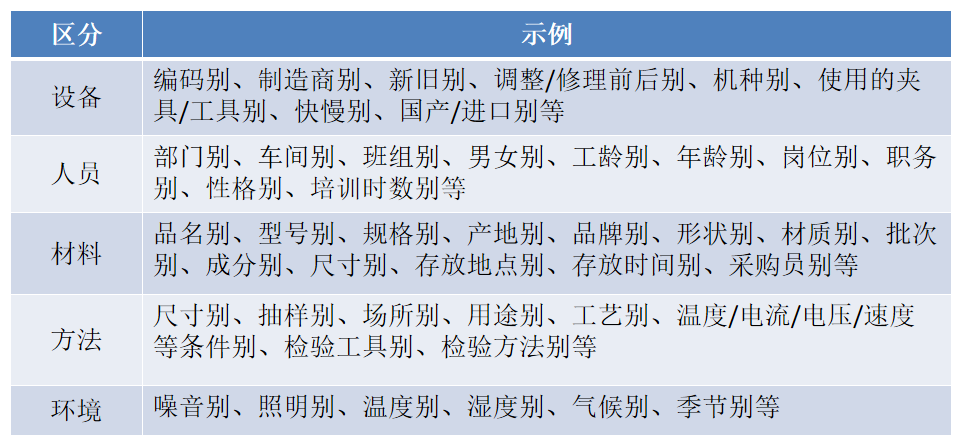
常见分层维度:
人(操作员) 机(设备) 材(批次) 法(工艺) 班组/时间段

QC Story与七大手法的结合应用
体现了一个更系统的应用思路:问题解决流程化、工具配套用。
步骤 | 工具 |
---|---|
把握现状 | 直方图、检查表 |
目标设定 | 柏拉图 |
要因分析 | 鱼骨图、散布图 |
对策实施 | 检查表、对策表 |
效果确认 | 控制图 |
标准化 | 文件管理 |
残留问题 | PDCA循环 |
这种结构化逻辑建议在企业内全面推行,帮助团队“从凭经验到靠工具”。
写在最后:会用工具的人,才能真正解决问题
QC七大手法,不是写报告时才掏出来摆样子的东西。它们是质检员、工程师、班组长用来发现、分析、解决问题的“日常武器”。
不要怕工具“看不懂”,只要你**每天用一点点,先从检查表、排列图做起,渐渐带上直方图、鱼骨图、控制图等,**你就能从“发现问题的人”,成长为“推动改善的人”。
--- END ---
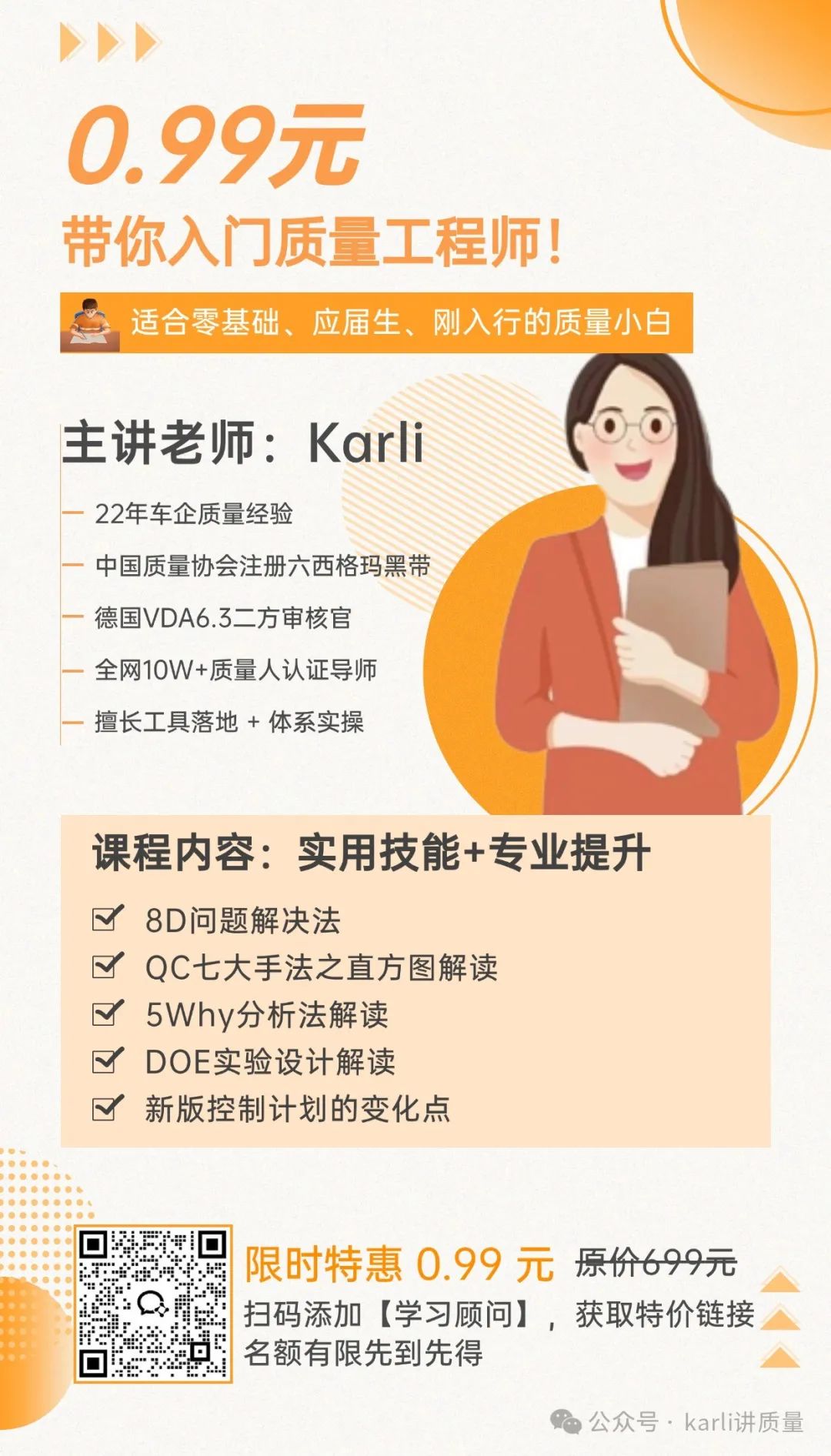
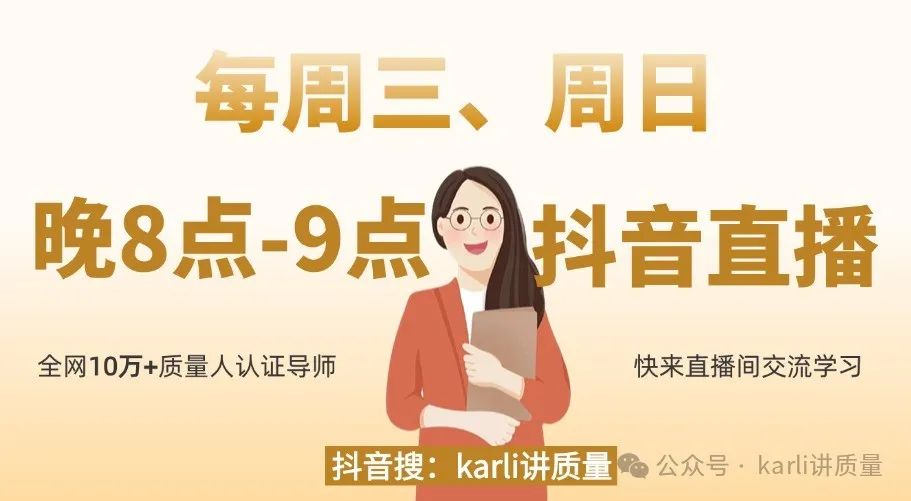